
So the best solution is to ensure the parts don't contain such volumes encased by a non-manifold surface in the first place. This is what happens when Meshmixer does just that: you are left with the cone half and some inverted artifact areas. Or even no more outer shell as the easiest solution is to just stitch that lower surface and discard the rest. This solution leads to two intersecting and manifold shells - a cylinder overlapping the drilled holes and the body with the drilled holes - which then promptly get treated with a boolean union. In the following picture, I have hidden part of the geometry to better show the problematic internal surfaces in orange:Īutomatic processes such as Meshmixer or Windows 10 3D builder interpret such an internal, one-sided open cylinder as "This probably is missing a surface on both ends". I will go to “Mesh Failure Diagnostics” and attempt to apply mesh control, but since it’s an imported part, I want to first run a Geometry Check.The body you modeled consists of a non-manifold shell: There exists a fully enclosed shell on the inside of the item that tries to define an "outside" of the body. As I try to mesh this part using the default mesh size, we can see that the SOLIDWORKS mesh error “failure to mesh part” has appeared. Starting with an imported model, we can run the diagnostic tool before setting up a static study. In this article, I will demonstrate how to suppress cosmetic features and suppress fillets and chamfers if they are not relevant to your analysis.
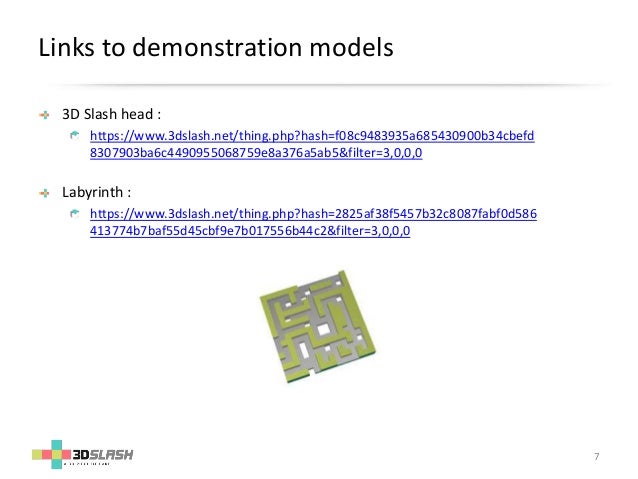
Based on your analysis objectives, you can suppress certain features that do not contribute to the results and are there for cosmetic reasons only.

The first step in debugging SOLIDWORKS mesh failures is looking at your geometry. When working with assemblies or complex parts you may experience SOLIDWORKS mesh failures or errors with messages like “mesh terminated” or “failure to mesh part” for certain features, or components.

Meshing is a crucial step for SOLIDWORKS Simulation.
